Develop innovative ideas for organisations, products or services
We support and fund organisations to innovate to encourage economic growth and create jobs.
We can help you to create new innovative ideas and improve existing products.
In Focus
We help businesses, the third sector, public sector bodies and research organisations to innovate and create new products and services. This can help increase commercialisation, improve skills and ensure Wales remains competitive and strives towards carbon-free in the future.
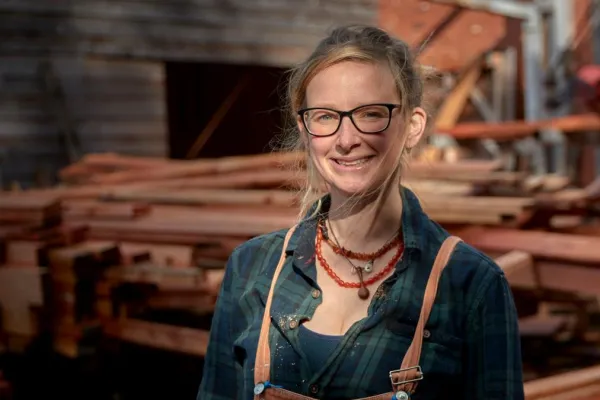
St. David’s Children Society reflect on their success following their participation in a Knowledge Transfer Partnership (KTP) which has helped them to streamline the adoption process.
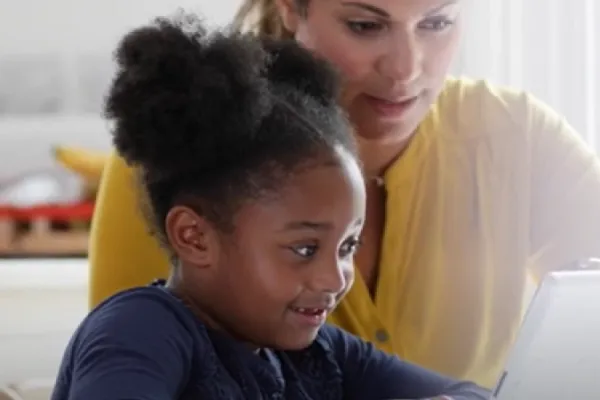
The Student Innovation Awards are a chance for young people to showcase their innovative ideas.

SMART FIS offers funding and technical support. See how Haydale thrived and how your organisation could too using SMART FIS support.
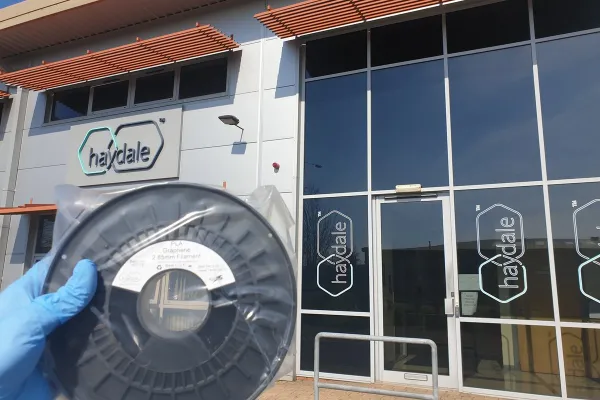
Down to Zero: Cynon Taf Community Housing Group takes an innovative approach to decarbonisation with the help of SMART partnerships.
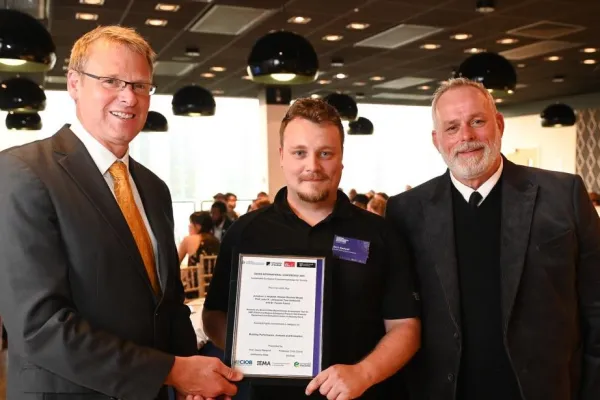
Is your business ready to innovate?
Access support from Business Wales
Innovation news



